Types of Heating Elements
Modern heated clothing represents a groundbreaking advancement in wearable technology, experiencing rapid adoption among winter sports enthusiasts and professionals working in extreme cold. The selection of heating elements plays a pivotal role in achieving the ideal combination of thermal efficiency, wearability, longevity, and value. This analysis provides a detailed examination of the four primary heating technologies employed in thermal garments, including a thorough evaluation of their respective benefits and limitations.
Composite Copper Wire
The composite heating wire consists of a core wire formed by the interwoven copper wire, nickel-chromium alloy wire of corresponding diameters, and cotton thread, along with an insulating layer covering the core wire. The electrothermal conversion is achieved by leveraging the resistance properties of the copper wire.
Advantages: The manufacturing process is mature. It has a high melting point and can automatically fuse to provide protection in case of a short circuit. The production cost is low.
Disadvantages: Copper wires are usually thick, which leads to low comfort. The electrothermal conversion efficiency is low, consuming more electrical energy and causing the battery to run out of power faster.
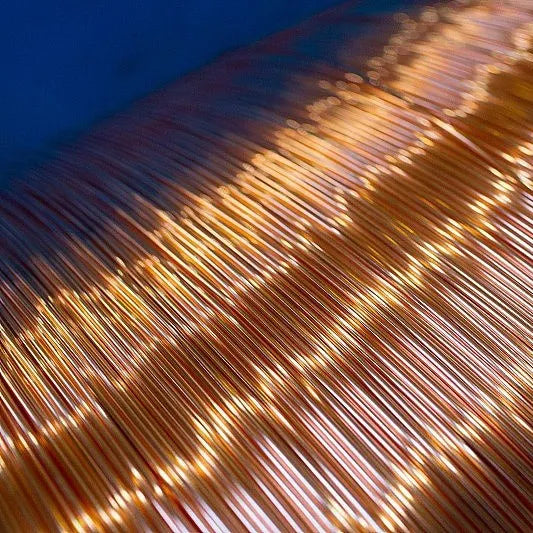
Carbon Fiber
A heating layer is woven with highly conductive carbon fiber filaments, which convert electrical energy into heat through the resistance effect.
Advantages: It has an extremely fast heating-up speed and can reach the set temperature within 5 - 10 seconds. The electrical energy conversion efficiency is over 80%, enabling longer battery life. Carbon fiber heating elements are thin, flexible, and lightweight, providing a comfortable and almost imperceptible wearing experience when embedded in clothing.
Disadvantages: Frequent movement may cause the carbon fibers to break, creating "cold spots" where heat is not generated locally, and the heat distribution may be uneven. The production cost of these components is high, making the related clothing relatively expensive.
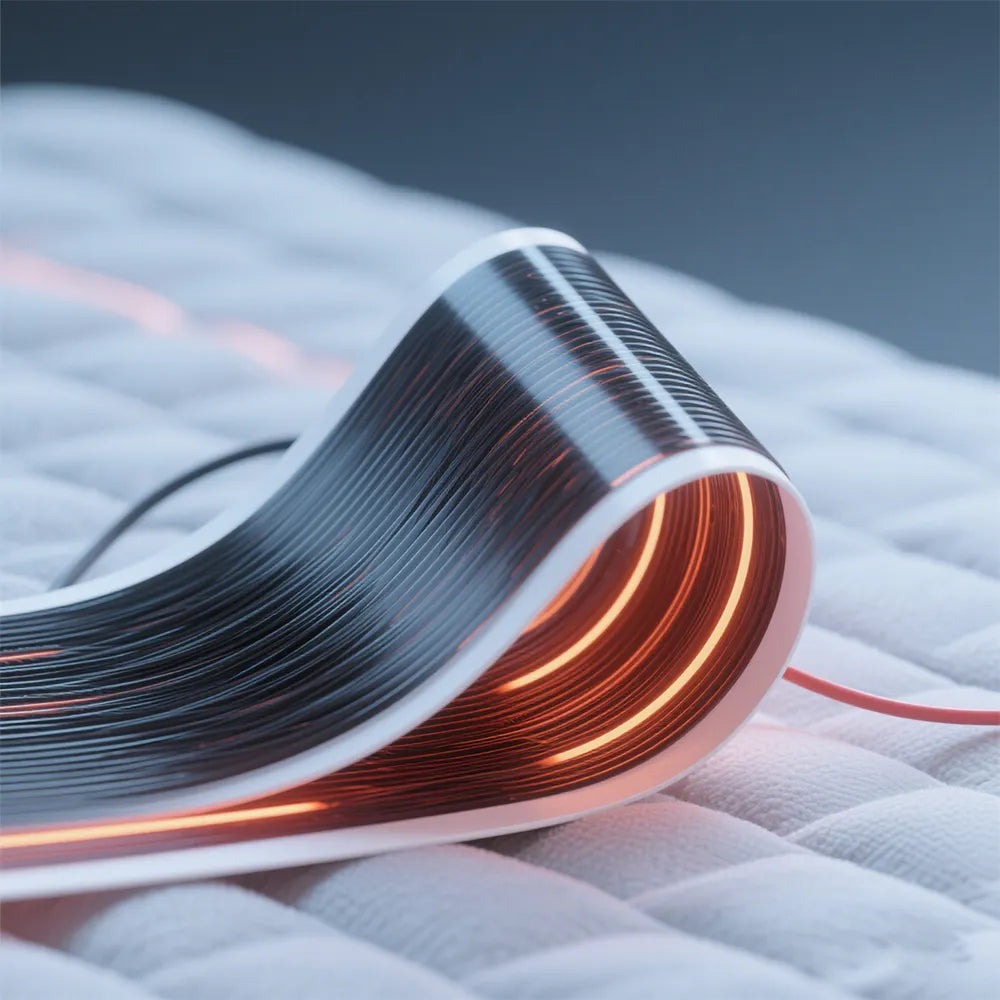
NanoCarbon Fiber
An even conductive layer is formed through a network of nanoscale carbon tubes to achieve efficient electrothermal conversion.
Advantages: With an ultra-thin design, the fibers are soft and flexible, ensuring a comfortable wearing experience. The uniformity of heat distribution is improved by 40%, avoiding local overheating. It can withstand 30 times of machine washing and the number of times it can endure bending exceeds 20,000.
Disadvantages: It has a high power consumption. The electrospinning process is complex, resulting in higher production costs.
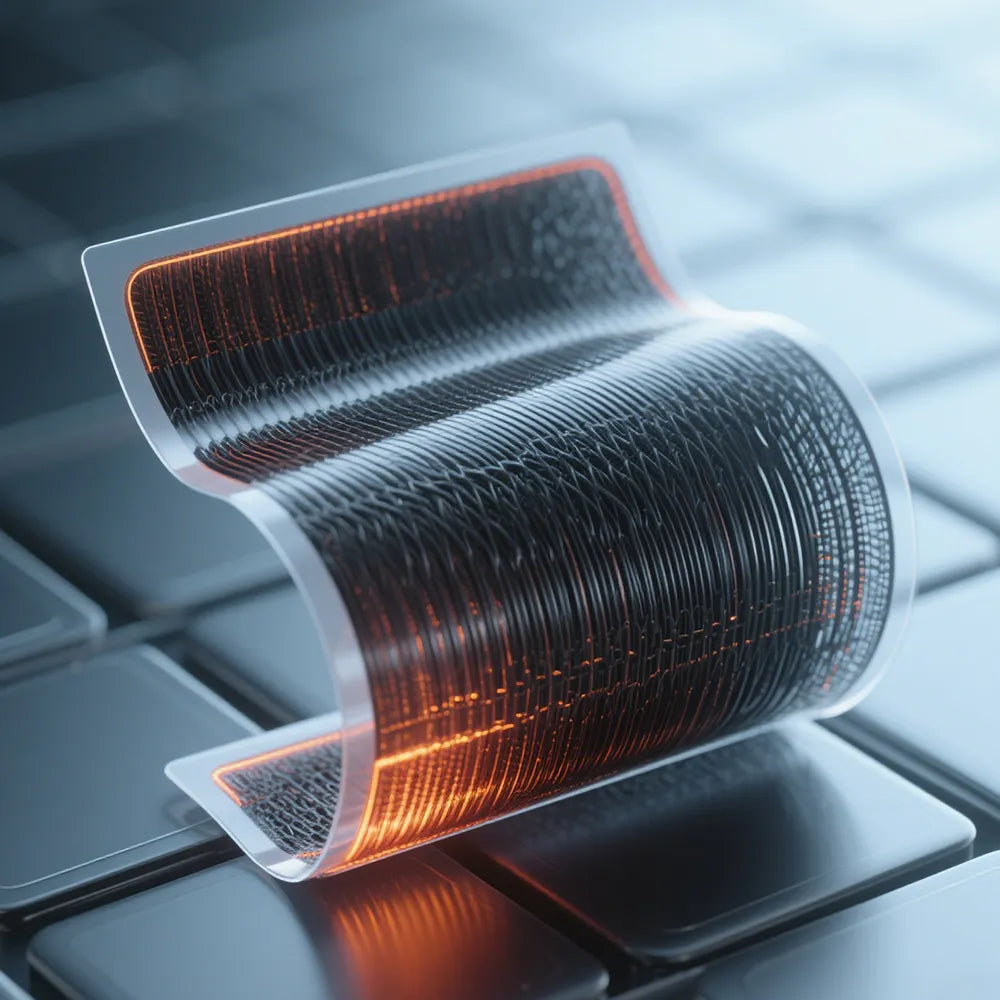
Conclusion
In heated apparel, selecting the appropriate heating element largely depends on the specific requirements of the garment and its intended use. ARRIS, one of the leading brands in heated clothing will continue to explore lighter, warmer, and smarter heating technologies to provide our customers with innovative heated products that combine both technology and style.